Client: Mercury Contracting Projects Ltd.
Location: St Julian’s, Malta
Sector: Residential/hotel
Architect: Zaha Hadid Architects
Structural Engineers: Evolve & BAC Engineering Consultancy Group
MEP Engineer: ECL Consulting Engineers
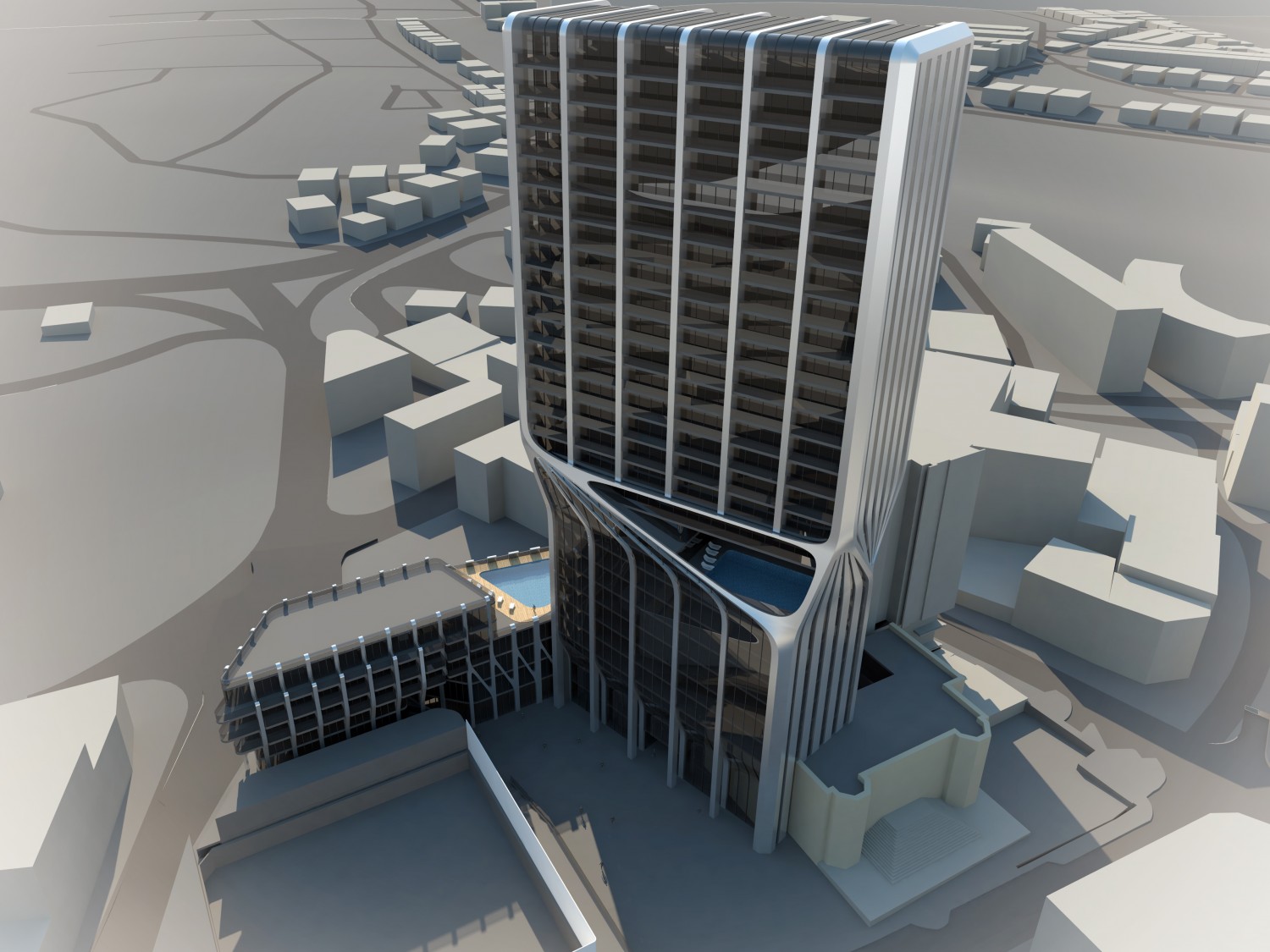
Challenge
The client for this project is a major investor and developer on Malta, with an enviable portfolio of properties across the island. This is his most prestigious project to date and one which he hopes will raise the bar in terms of quality and specification for residential developments in St Julian’s. His selection of a world-famous architect clearly set out his intentions, with a brief to create a truly iconic site.
The Phase One tower is undoubtedly the most prominent feature and its form, with striking vertical lines and unique twist, will set it apart from anything else on the Island. The choice of cladding material will also differentiate it from the numerous limestone façades in the neighbourhood, whilst Phase Two introduces some contrasting greenery to the area and striking, bright open spaces.
The towers are not abnormally slender in overall footprint, but their core and column layout has been tightly controlled to suit the architecture, thus maximising net areas within the town planning envelope and site constraints, whilst respecting the requirements of all levels from high level apartments, mid height twist and leisure spaces, ground floor retail and subterranean car parking.
The net result led the structural design towards a solution which combines the rigidity of the core walls with the portal frame action possible with deep column sections. This aligns perfectly with the architecture which uses the deep columns to separate the apartments, defining their balconies and outside spaces.
Solution
The choice of materials for the structure was made after thorough discussions with the client and his in-house construction team. In situ reinforced concrete was selected to make best use of the existing skill set and available labour resource on the island. A corresponding selection of formwork systems and raw materials was also made to best suit the project. The client team’s expertise was structured to include the best local managers available together with construction experts with relevant high-rise experience abroad. Best practice learnt from London and the Middle East was duly considered. Formwork market leaders, Peri, were introduced to the project and the design developed around their lightweight DUO formwork slab support system. The cores were developed to suit their input and jumpform proposals. Aggregate selection was carefully considered and developed to maximise the use of local materials, with extensive material testing undertaken to develop mixes which would suit the relatively high strengths proposed to optimise the structure. Quality Control procedures were established from the outset combining local expertise from Terracore and the provision of full-time resident engineering support from our Spanish partners BAC.
The construction of the six-storey basement obviously had its challenges but did benefit from the limestone bedrock prevalent across the site and throughout this part of the Island. Vertical faces could be cut with large vehicle mounted circular saws and the limestone could then be broken and removed from site for recycling
as construction materials elsewhere. Occasional faults in the rock were encountered during the dig so ties and anchors were installed under the guidance of the local geotechnical engineer experienced with this material.
The number of basement levels was determined based on the local groundwater or ‘sea’ level. The excellent bearing capacity of the limestone meant that structure could be founded on relatively small concrete pad foundations, albeit all carefully specified to take account of the aggressive sea water conditions.
Because of the limited rainfall on the island, all developments are obliged to store considerable volumes of rainwater and subterranean tanks were included effectively at B7 level.
Although the structure is essentially concrete, some key elements have been developed to include structural steel sections and frames where appropriate. The most notable steel element is provided as a three-storey deep, three-dimensional truss structure at the twist. The design for this steelwork has been carefully developed to coordinate with the base concrete structure and to take advantage of the preceding core construction to minimise temporary works. This is particularly important bearing in mind the 6-7m adjustment on plan of some columns and floor edges, all 50-60m above ground level below.
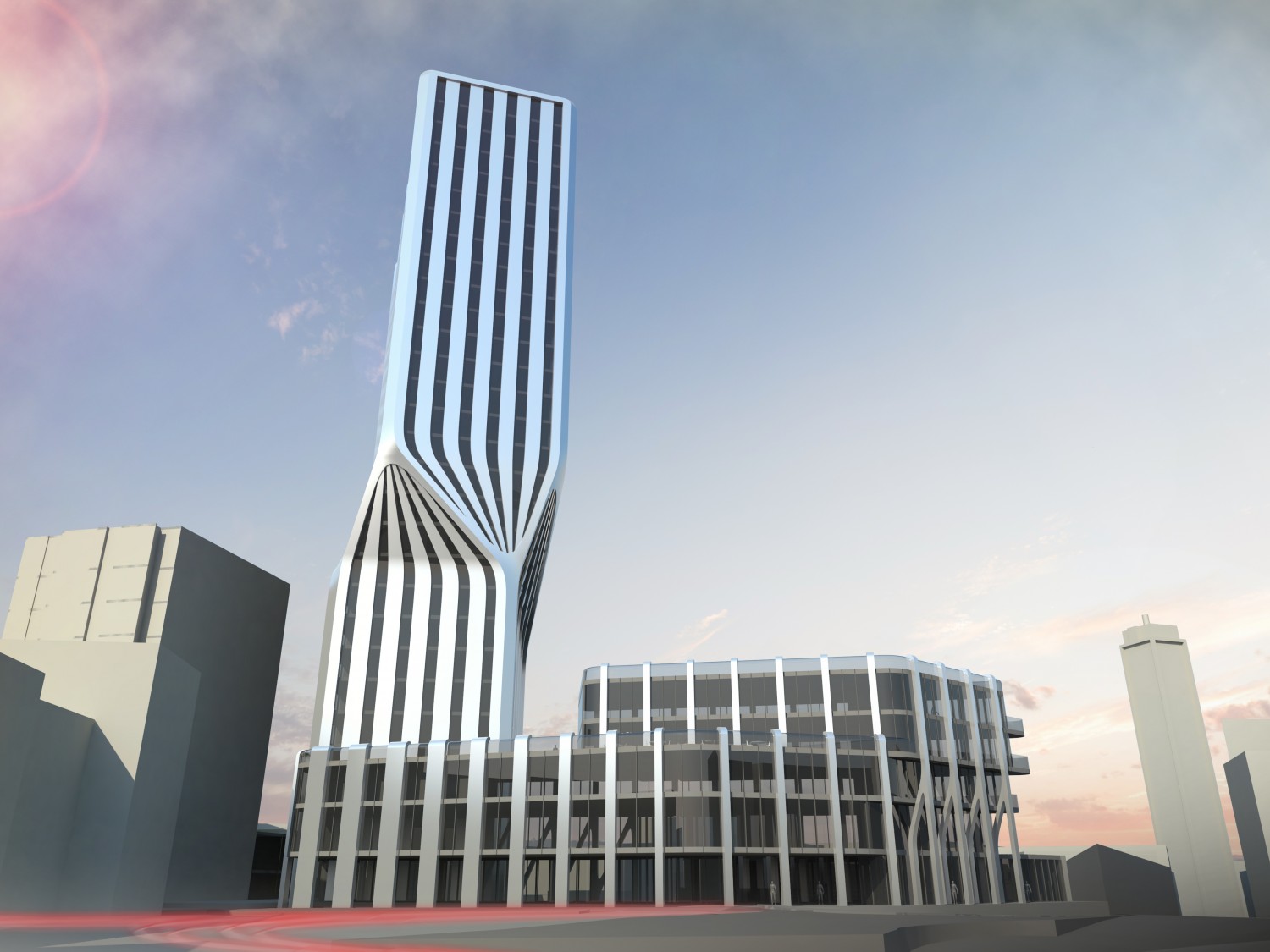